Understanding the design and functionality of a die casting mold is critical for ensuring that the final product meets unique manufacturing requirements. By selecting or designing the right die casting mold on Junying, manufacturers can achieve greater precision, efficiency, and quality in their production processes.
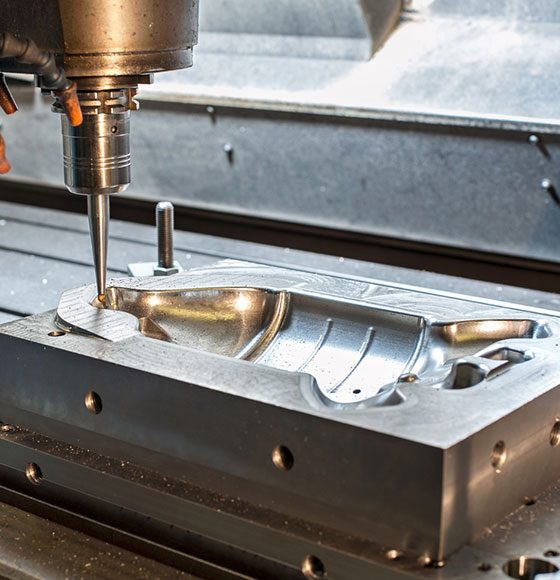
Types of Die Cast Tooling
There are several types of die cast tooling, each designed for specific applications and production needs. Common types include:
- Single-Cavity Mold: Used for producing one part per cycle, ideal for low-volume production.
Multi-Cavity Mold: Designed to produce multiple identical parts in one cycle, increasing efficiency.
Unit Die Mold: A flexible option that allows for interchangeable inserts to create different parts.
Family Mold: Produces different parts in one cycle, suitable for assemblies requiring multiple components.
How to Design a Die Casting Mold
Designing a die casting mold involves several critical steps to ensure optimal performance and efficiency. Here are some key considerations:
Understand the Product Requirements: Define the dimensions, material properties, and functionality of the part to be manufactured.
Select the Mold Material: Choose a durable material capable of withstanding high temperatures and pressures, such as tool steel.
Design the Mold Cavity: Create a precise cavity that reflects the desired shape and features of the final product.
Incorporate Cooling Systems: Integrate cooling channels to ensure consistent temperature control during the casting process.
Plan for Venting: Include venting systems to allow trapped air to escape, preventing defects in the cast.
Proper mold design is essential for achieving high-quality results and reducing production costs.
Factors to Consider When Choosing a Die Casting Mold
Selecting the right mold involves evaluating several factors, such as:
Production Volume: High-volume production requires durable molds that can withstand extended use.
Part Complexity: Complex parts may require advanced mold designs with intricate features.
Material Compatibility: Ensure the mold material is compatible with the casting material.
Cost: Balance upfront mold costs with long-term production efficiency and durability.
Lead Time: Consider the time required to design, manufacture, and test the mold.
By addressing these factors, manufacturers can choose molds that align with their specific needs and goals.
Applications of Die Casting Molds
Die casting molds are used in various industries, including automotive, aerospace, electronics, and consumer goods. For instance, molds can be designed to create intricate components for golf equipment, ensuring precision and performance. By leveraging advanced mold designs, manufacturers can produce high-quality parts that meet industry standards.
To explore and buy die casting molds, visit trusted suppliers diecasting-mould.com for reliable solutions.
For more information about designing and purchasing die casting molds, visit Die Casting Mould. Enhance your manufacturing processes with precision-engineered molds.